Quenching is a heat treatment process in which steel castings are heated to a temperature above Ac3 or Ac1, and then rapidly cooled after holding for a period of time to obtain a complete martensitic structure. The steel castings should be tempered in time to eliminate the quenching stress and obtain the required comprehensive mechanical properties. Therefore, the tempering heat treatment is usually used after the queching. The are also called QT. The other common used heat treatment include annealing, normalizing and solid solution.
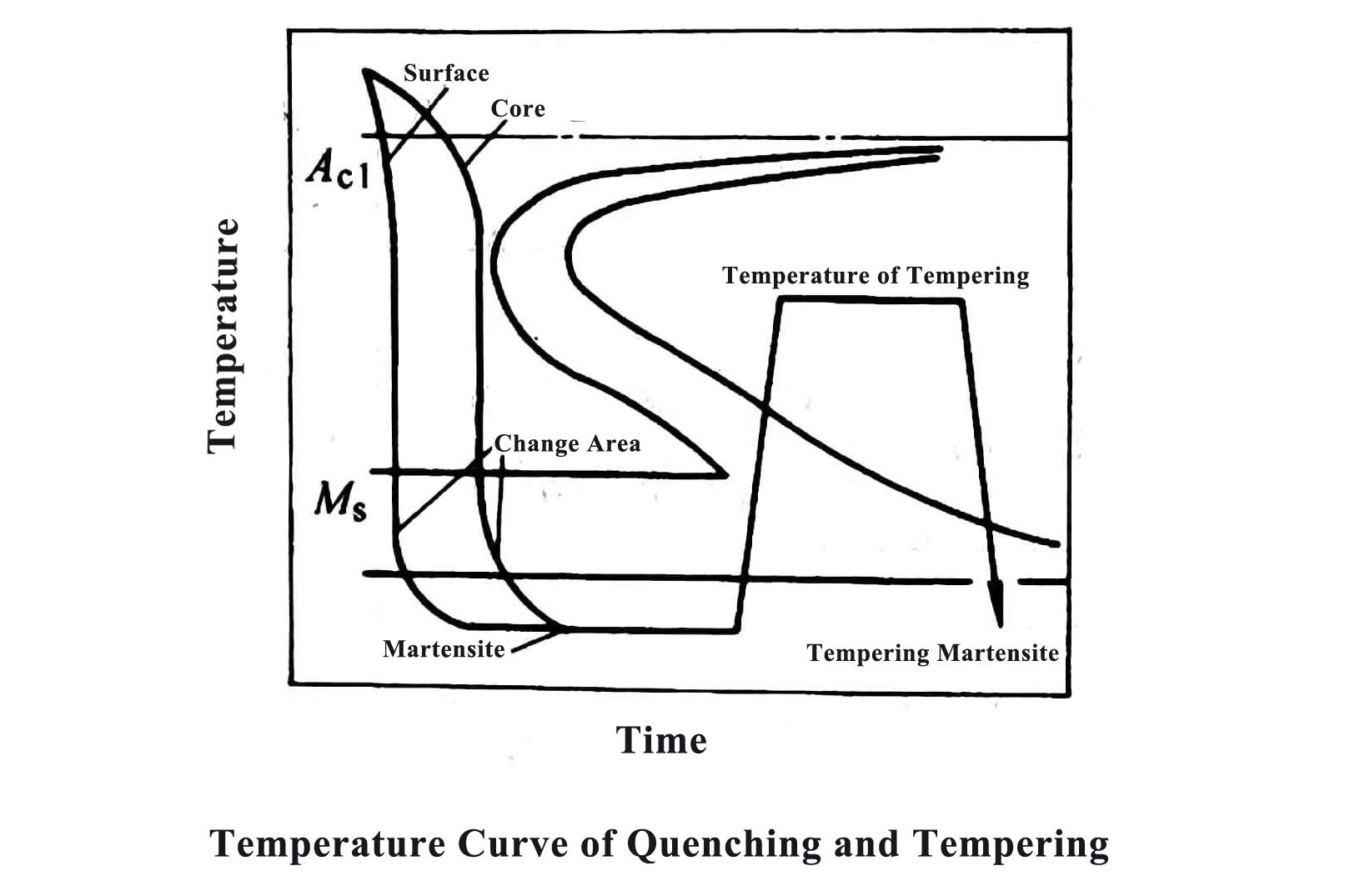
QUENCHING
1. Quenching TemperatureThe quenching heating temperature of hypoeutectoid steel is 30℃-50℃ above Ac3; the quenching heating temperature of eutectoid steel and hypereutectoid steel is 30℃-50℃ above Ac1. Hypoeutectoid carbon steel is heated at the above-mentioned quenching temperature in order to obtain fine grained austenite, and fine martensite structure can be obtained after quenching. The eutectoid steel and hypereutectoid steel have been spheroidized and annealed before the quenching and heating, so after heating to 30℃-50℃ above Ac1 and incompletely austenitized, the structure is austenite and partially undissolved fine-grained infiltration Carbon body particles. After quenching, austenite is transformed into martensite, and undissolved cementite particles are retained. Due to the high hardness of cementite, it not only does not reduce the hardness of steel, but also improves its wear resistance. The normal quenched structure of hypereutectoid steel is fine flaky martensite, and fine granular cementite and a small amount of retained austenite are evenly distributed on the matrix. This structure has high strength and wear resistance, but also has a certain degree of toughness.
2. Cooling Medium for Quenching Heat Treatment Process
The purpose of quenching is to obtain complete martensite. Therefore, the cooling rate of the cast steel during quenching must be greater than the critical cooling rate of the cast steel, otherwise the martensite structure and corresponding properties cannot be obtained. However, too high a cooling rate can easily lead to deformation or cracking of the casting. In order to meet the above requirements at the same time, the appropriate cooling medium should be selected according to the material of the casting, or the method of staged cooling should be adopted. In the temperature range of 650℃-400℃, the isothermal transformation rate of supercooled austenite of steel is the largest. Therefore, when the casting is quenched, rapid cooling should be ensured in this temperature range. Below the Ms point, the cooling rate should be slower to prevent deformation or cracking. Quenching medium usually adopts water, aqueous solution or oil. In the stage quenching or austempering, the commonly used media include hot oil, molten metal, molten salt or molten alkali.
The cooling capacity of water in the high temperature zone of 650℃-550℃ is strong, and the cooling capacity of water in the low temperature zone of 300℃-200℃ is very strong. Water is more suitable for quenching and cooling of carbon steel castings with simple shapes and large cross-sections. When used for quenching and cooling, the water temperature is generally not higher than 30°C. Therefore, it is generally adopted to strengthen the water circulation to keep the water temperature within a reasonable range. In addition, heating salt (NaCl) or alkali (NaOH) in water will greatly increase the cooling capacity of the solution.
The main advantage of oil as a cooling medium is that the cooling rate in the low temperature zone of 300℃-200℃ is much lower than that of water, which can greatly reduce the internal stress of the quenched workpiece and reduce the possibility of deformation and cracking of the casting. At the same time, the cooling capacity of oil in the high temperature range of 650℃-550℃ is relatively low, which is also the main disadvantage of oil as a quenching medium. The temperature of quenching oil is generally controlled at 60℃-80℃. Oil is mainly used for the quenching of alloy steel castings with complex shapes and the quenching of carbon steel castings with small cross-sections and complex shapes.
In addition, molten salt is also commonly used as a quenching medium, which becomes a salt bath at this time. The salt bath is characterized by a high boiling point and its cooling capacity is between water and oil. Salt bath is often used for austempering and stage quenching, as well as for the treatment of castings with complex shapes, small dimensions and strict deformation requirements.
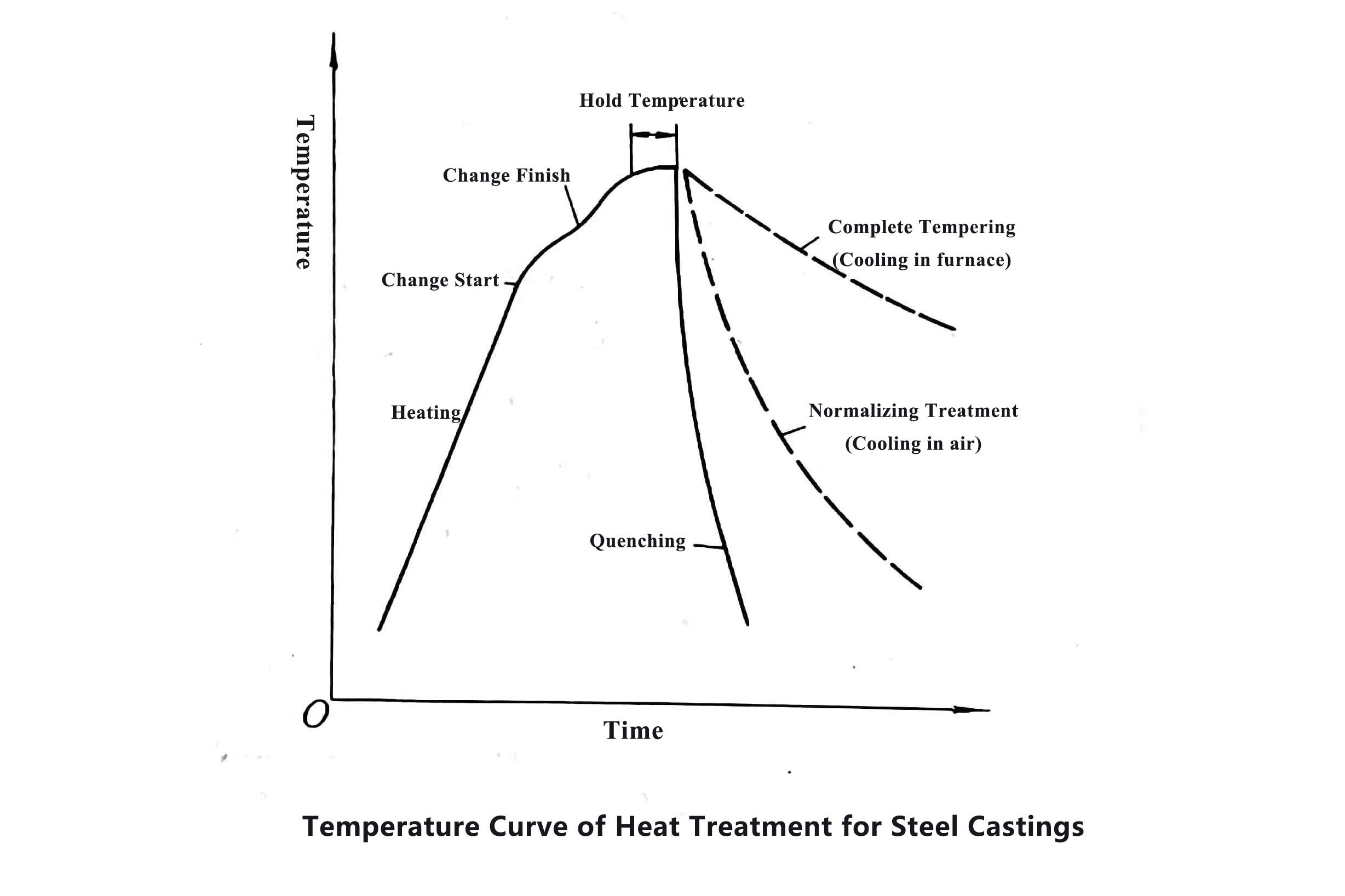
TEMPERING
Tempering refers to a heat treatment process in which the quenched or normalized steel castings are heated to a selected temperature lower than the critical point Ac1, and after holding for a period of time, they are cooled at an appropriate rate. Tempering heat treatment can transform the unstable structure obtained after quenching or normalizing into a stable structure to eliminate stress and improve the plasticity and toughness of steel castings. Generally, the heat treatment process of quenching and high temperature tempering treatment is called quenching and tempering treatment. The quenched steel castings must be tempered in time, and the normalized steel castings should be tempered when necessary. The performance of steel castings after tempering depends on the tempering temperature, time and number of times. The increase of tempering temperature and the extension of holding time at any time can not only relieve the quenching stress of steel castings, but also transform unstable quenched martensite into tempered martensite, troostite or sorbite. The strength and hardness of steel castings are reduced, and the plasticity is significantly improved. For some medium alloy steels with alloying elements that strongly form carbides (such as chromium, molybdenum, vanadium and tungsten, etc.), the hardness increases and toughness decreases when tempering at 400℃-500℃. This phenomenon is called secondary hardening, that is, the hardness of the cast steel in the tempered state reaches the maximum. In actual production, medium alloy cast steel with secondary hardening characteristics needs to be tempered many times.THE EFFECT OF QT ON STEEL CASTINGS
In addition to the performance of steel castings depending on the chemical composition and casting process, different heat treatment methods can also be used to make it have excellent comprehensive mechanical properties. The general purpose of the heat treatment process is to improve the quality of the castings, reduce the weight of the castings, extend the service life and reduce costs. Heat treatment is an important means to improve the mechanical properties of castings; the mechanical properties of castings are an important indicator for judging the effect of heat treatment. In addition to the following properties, the foundry must also consider factors such as processing procedures, cutting performance and the use requirements of the castings when heat-treating steel castings.
1. The Influence of QT on the Strength of Castings
Under the condition of the same cast steel composition, the strength of steel castings after different heat treatment processes has a tendency to increase. Generally speaking, the tensile strength of carbon steel castings and low alloy steel castings can reach 414 Mpa-1724 MPa after quenching and tempering.
2. The Effect of QT on the Plasticity of Steel Castings
The as-cast structure of the steel castings is coarse and the plasticity is low. After heat treatment, its microstructure and plasticity will be improved accordingly. Especially the plasticity of steel castings after quenching and tempering treatment (quenching + high temperature tempering) will be significantly improved.
3. The Influence of Quenching and Tempering on the Toughness of Steel Castings
The toughness index of steel castings is often evaluated by impact tests. Since the strength and toughness of steel castings are a pair of contradictory indicators, the foundry must make comprehensive considerations to select a suitable heat treatment process in order to achieve the comprehensive mechanical properties required by customers.
4. The Effect of QT on the Hardness of Castings
When the hardenability of the cast steel is the same, the hardness of the cast steel after heat treatment can roughly reflect the strength of the cast steel. Therefore, the hardness can be used as an intuitive index to estimate the performance of cast steel after heat treatment. Generally speaking, the hardness of carbon steel castings can reach 120 HBW - 280 HBW after heat treatment.
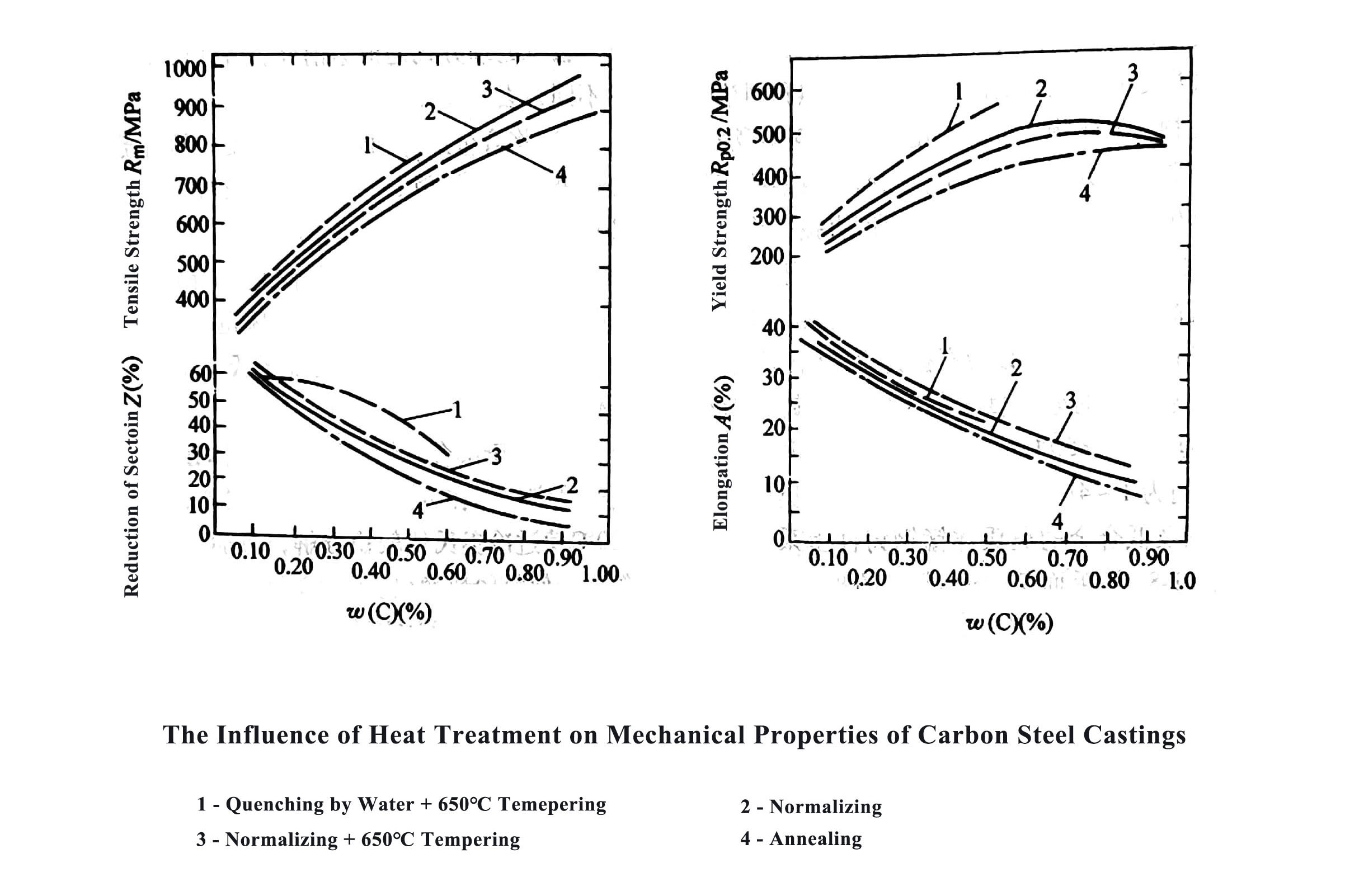