A foundry is a professional factory specializing in the production of various metal castings. Different foundries have their own casting processes, such as sand casting, investment casting, shell molding casting, lost foam casting, vacuum casting and die casting. Depending on the real casting capability, a foundry is always could cast or pour more than one kind of metals and alloys, from cast iron, cast steel, stainless steel, brass, bronze and aluminium alloys. However, the basic functional composition of the foundry should be roughly the same.
A typical sand casting foundry should have these basic departments:
• Comprehensive Management Department
• Research, Design and Development Department
• Purchasing Department
• Production Department (including molding workshop, sand core making workshop, sand processing workshop, metal melting workshop, casting cleaning workshop)
• Quality Inspection Department
• Storage Department
• Equipment Maintenance Department
It can be seen that the production department, especially the molding workshop, is the most important and core department of the foundry, and they play a vital role in casting production.
This article will introduce which departments and their functions should a typical foundry have. This article mainly takes sand casting foundry (a foundry which is focusing on sand casting process) as example, and by the way other processes (investment casting, coated sand casting, lost foam casting, vacuum casting, etc.) are briefly introduced.
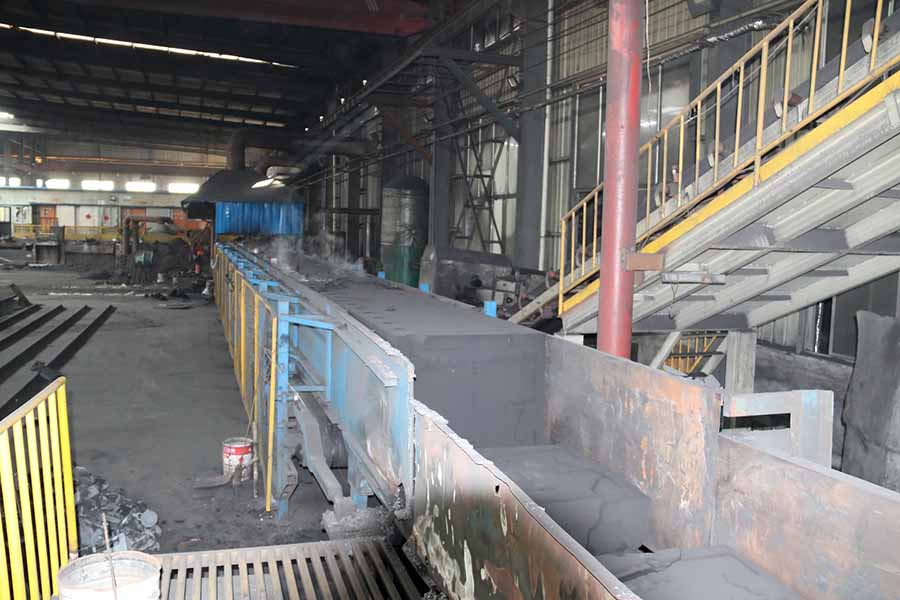
1 Comprehensive Management Department
The function of the foundry's integrated management department is to coordinate and manage the work of all departments in the entire foundry. It is the basic guarantee for the normal and orderly operation of the foundry.
2 Research, Design and Development Department
The design and development department of the foundry is mainly responsible for the research and development of the drawing design, material selection, mold design, inspection tool design and various production tooling of castings. This department is also responsible for communicating technical requirements with purchasers or end users, and trying its best to meet user needs and put forward corresponding technical suggestions.
3 Purchasing Department
The Purchasing Department is mainly responsible for purchasing various raw materials including modeling materials, auxiliary tools, scrap steel, scrap iron, metals containing trace elements, etc., to meet the material needs of the production department and other departments. At the same time, the foundry needs to add new equipment, tools, etc., and the purchasing department also needs to purchase from the foundry's suppliers.
4 Production Department
1) Molding Workshop
The molding workshop is the most important workshop of the foundry, and the quality of the molding is directly related to the quality of the final casting. The main production processes of the molding workshop include: molding, core setting, molding, casting, cooling and sand falling.
In casting production, the liquid metal from the metal melting workshop, the sand core from the core making workshop and the molding sand from the sand processing workshop all arrive at the molding workshop. Then complete the mold assembly and liquid metal casting in the molding workshop.
Most of the foundries in China are already using automatic molding production lines with a relatively high degree of mechanization. In the foundry of RMC, there are two automatic molding lines, a vertical automatic molding production line and a horizontal automatic molding production line.
2) Sand Core Making Workshop
The task of the core workshop is to produce qualified sand cores. It generally has these processes: raw material procurement, sand mixing (through sand mixer), core making (through core shooter), hardening (drying), grinding, assembly, coating, secondary drying, transportation and storage core.
Depending on the adhesive used when making the core, the core making method and equipment used are also different. Generally speaking, the core-making process can be divided into the following categories:
• For clay sand, oil sand and grease sand, the sand core is formed in the core box. After taking out the sand core, put it into the drying furnace for drying.
• For shell core modeling, the heating and hardening of the sand core are done in the core box
• For self-hardening sand cores, the sand cores are placed in a core box and harden to the shape of the core by themselves when placed at room temperature.
3) Sand Processing Workshop
The task of the sand processing workshop is to provide molding sand and core sand that meet certain requirements required by the molding and core making workshop. In the sand processing workshop, the sand mixer is the core equipment. Different molding sand and core sand (such as clay sand, sodium silicate sand, resin sand, etc.) must use different sand mixers, and the corresponding sand processing procedures are different.
The characteristics of the sand processing workshop make the types of raw materials, large consumption, large transportation volume, and complicated management and scheduling. At the same time, the sand processing workshop produces a lot of dust pollution. Therefore, the sand treatment workshop generally needs to use mechanized equipment and install dust collectors and other equipment to clean the exhaust gas.
4) Metal Melting Workshop
The task of the metal melting workshop is to provide qualified liquid metal for casting. The raw materials required for metal melting include scrap steel, scrap iron, pouring riser scrap, pouring riser scrap, coke, limestone and alloys containing trace elements. Before the formal casting, it is necessary to analyze the chemical composition of the molten metal in the furnace to ensure that the molten metal can meet the required chemical composition.
Electric furnace is the main equipment of metal melting workshop. In foundries, medium frequency induction furnaces, electric arc furnaces and resistance furnaces are generally used. Choose the appropriate electric furnace type for different metals.
5) Casting Cleaning Workshop
The main task of the casting cleaning workshop is to remove the castings' gates and risers, clean the surface of the castings and repair the defects of the castings. The equipment used to clean the castings should be selected according to the type of casting alloy, the shape, size, weight and complexity of the casting.
Different types of castings should choose different types of casting cleaning equipment. In foundries, commonly used casting cleaning equipment are: shot blasting machine, sandblasting machine, sandblasting room, grinding machine, cutting machine, vibration equipment, dust collector and so on.
5 Quality Inspection Department
Quality inspection runs through every link of the casting production process and is the line of defense to ensure qualified castings. Therefore, the quality inspection of castings must be done in strict accordance with the process requirements. The main inspection items of the Quality Inspection Department include but are not limited to: incoming material inspection, process inspection, furnace chemical element inspection, casting internal inspection, metallographic inspection, casting mechanical property inspection, casting size inspection, etc.
Quality inspection instruments are necessary equipment for casting to ensure product qualification. Take RMC foundry as an example, our quality inspection equipment includes: Metallographic Detector, Spectrum Scanner, CMM, Hardness Tester, Yield Strength Tester, Tensile Strength Tester, Vernier Caliper, Dynamic Balance Tester, etc. .
6 Storage Department
Since the foundry uses kinds of raw materials (metals, fuel, refractory materials, molding materials, solvents, binders, etc.) at a large quantities, special raw material warehouses are required. At the same time, the castings produced by the foundry and the mechanical equipment and tools used should also be stored.
Generally speaking, the storage area of a foundry includes: furnace materials warehouse, molds warehouse materials, finished castings warehouse, tools warehouse and process equipment warehouse.
7 Equipment Maintenance Department
The modern foundry has a wide variety of casting machinery and equipment, and the various production processes are inter-connected. Any failure of one piece of equipment may affect the production schedule of the entire foundry. Therefore, the maintenance and maintenance of casting equipment must be strengthened. The department also needs to inspect, repair and maintain the power system and water supply and drainage system of the foundry.
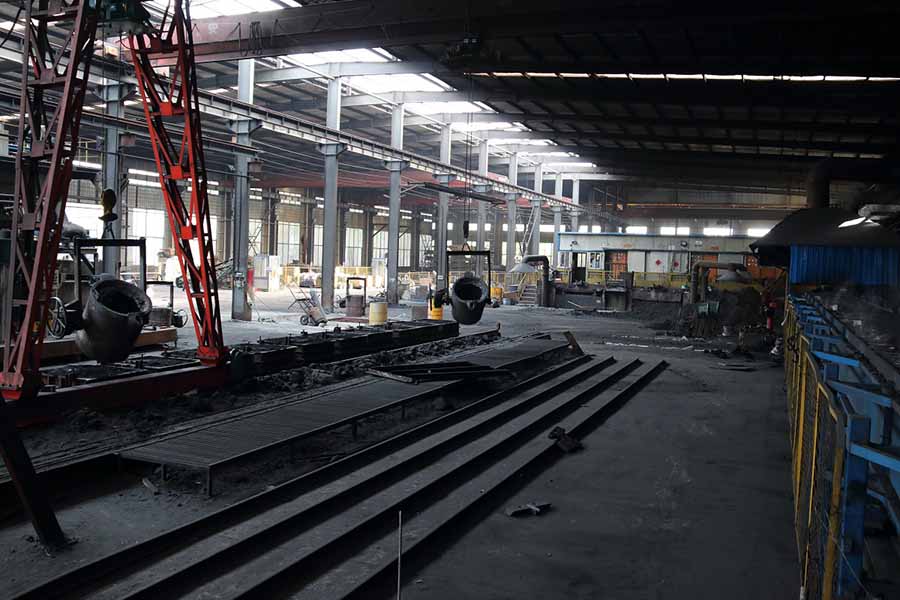